Electric cars: Will silicon anodes be the next breakthrough?
Silicon anodes could greatly improve battery performance in electric cars. They absorb a lot of lithium, but that also have a weakness.
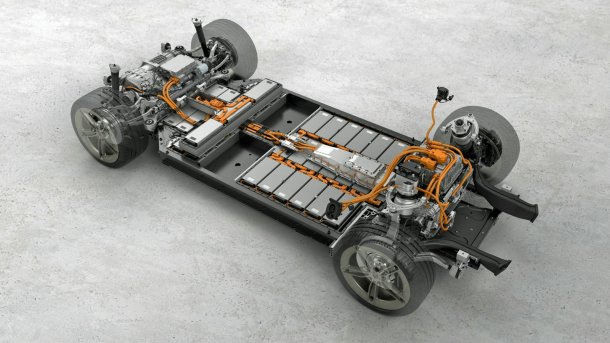
Together with the Audi e-tron GT on the same platform (J1), the Porsche Taycan is currently the only electric car that does not have an anode consisting exclusively of graphite. Instead, a single-digit percentage of silicon is added to the graphite. Silicon can absorb much more lithium than graphite and has the potential to significantly improve charging performance and energy density.
(Bild: Porsche)
- Christoph M. Schwarzer
No revolution yet, but evolution continues: Batteries in electric cars provide higher energy density and charging capacity is gradually increasing. There's further potential in improving battery cell anodes, which are mostly made with graphite. In its Taycan model, Porsche uses batteries five percent silicon in the anodes. Anodes made of pure silicon offer great advantages in almost every respect – provided that some problems can be solved.
There is a simple reason why almost all lithium-based battery cells have a graphite anode, regardless of the cathode material: graphite has proven its worth. Chemically, it is simply carbon. The service life is long and energy density acceptable. An industrial policy risk, on the other hand, is the dependence on China, where over 90 percent of global production capacity is concentrated. Furthermore, graphite requires a lot of volume and is currently the most important factor in limiting the charging rate. In addition, frequent fast charging favors the deposition of lithium (lithium plating), which greatly reduces durability and can become a safety problem.
(Bild: NorcSi)
Silicon can absorb much more lithium
The electrochemical strength of silicon is that one atom of silicon can absorb up to 3.5 atoms of lithium. However, six carbon atoms are required to absorb one atom of lithium. However, silicon is heavier than carbon, which counteracts this advantage. A battery cell with a pure silicon anode would therefore have a much higher volumetric energy density, which experts estimate at over 1000 watt hours per liter, where today 600 Wh/l are common. The advantage in terms of gravimetric energy density could also be around 50 percent, for example 375 instead of the current 250 watt hours per kilogram. A traction battery with a silicon anode would therefore be considerably smaller and lighter than a storage unit with a graphite anode, but with the same energy content.
(Bild: NorcSi)
Material stress due to volume change
In practice, the problem with silicon is the very strong expansion and contraction when charging and discharging the battery. This permanent change in volume means enormous material stress and consequently wear. This can be controlled by adding a small amount of silicon to graphite, as Porsche does, but the ideal energy density and charge rate cannot be achieved or can only be partially achieved in this way. Research and industry are working on different processes to guarantee the stability of a pure silicon anode. NorcSi, a kind of atypical start-up from Halle (Saale), has developed a promising, foreseeably inexpensive and patented process. It employs 14 people, from laboratory technicians to scientists.
(Bild: Volkswagen)
Structure like reinforced concrete
NorcSi combines two well-known and proven processes. One is roll-to-roll production. A copper carrier foil is coated with a thin layer of pure silicon. Unlike metallic lithium, for example, silicon is easy to handle and the current production technology would only need to be modified. The highlight of NorcSi's process is the subsequent flash lamp annealing. In flash lamp annealing (FLA for short), which lasts just milliseconds, the brief heating causes dendrites to grow from the copper foil into the silicon. They form a mechanically stabilizing structure, similar to steel in concrete. At the same time, the conductivity is similar to that of metal. A top protective layer, which is applied on top, is intended to minimize lithium deposition.
Cycle stability not yet sufficient
This anode expands during the first charge; after that, the change in volume should be comparatively small. The material stress is manageable. The cyclic durability in the laboratory is already 300 to 400 cycles; an increase to large-scale production requirements should be feasible. A pure silicon anode could therefore be produced in a relatively simple and correspondingly cost-effective production process. Because the layer thickness is 90 percent less than that of graphite, it has very good electrical and thermal conductivity. Not to forget: both copper and silicon are easy to recycle.
(Bild: NorcSi)
Competition between the processes
Prof. Dr. Markus Hölzle from the ZSW (Centre for Solar Energy and Hydrogen Research) in Baden-Württemberg is a materials specialist. He heads the Electrochemical Energy Technologies division at the ZSW and classifies the NorcSi process: "The method for structure formation, electrical bonding and the containment of lithium deposition is comprehensible and credible," says Hölzle. But: "Silicon is difficult to tame," explains Professor Hölzle, and its durability has yet to be proven. There are doubts here. Nevertheless, companies around the world are working on it. However, not all of them are at the same level as NorcSi. Graphenex Development Inc (GDI), for example, has received a loan of 20 million euros from the European Investment Bank (EIB). GDI also wants to produce a pure silicon anode.
Opportunity for European value creation
The raw material silicon could not only increase the charging capacity. Ten minutes for the hub from ten to 80 percent should be realistically achievable. Increased use of silicon would also reduce dependence on China. In the NorcSi process, for example, low grade instead of high-purity silicon is sufficient, which in turn reduces costs and makes the supply chain less complicated. The next car manufacturer after Porsche and Audi (Taycan and e-tron GT) to announce an anode with an admixture of silicon is Mercedes: the upcoming CLA, which was shown as a study at the IAA in Munich, will use this cell chemistry from 2025. In combination with the 800-volt platform, buyers can therefore look forward to a potentially short charging stop.
If an anode with pure silicon can be optimized for series production, this would be a significant advance for the traction battery in electric cars. In terms of properties, this cell chemistry has the potential to come close to the values of real solid-state batteries with a metallic lithium anode, but without the difficulties of handling and costs. Simplicity and affordability have long been key factors in the spread of cell chemistry. In addition, the strategic dependence on China would decrease and value creation could take place in Europe.
More about electric cars
ICCT Global Automaker Rating 2023: The fastest on the road to e-mobility
E-Cars: Germany plans mandatory charging points for gas stations
Electric and hybrid cars: only less than 40 % battery charge on Greek ferries
Up to 100 per cent duty for e-cars from China in the USA
E-cars: BMW admits to environmental problems at Moroccan cobalt mine
(vbr)